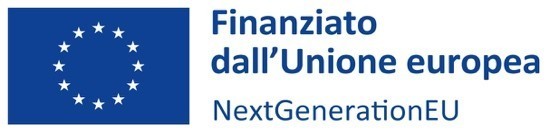
nome dell'impresa
Gaser Ossido Duro srl
titolo del progetto
Digital Twin di un impianto di ossidazione per supportare la schedulazione e l'ottimizzazione del processo
dimensione e localizzazione
Media impresa - Rozzano (MI)
competenze utilizzate
Gaser Ossido Duro srl, da oltre 50 anni, è un’azienda leader nel settore dei trattamenti superficiali per metalli, offrendo soluzioni innovative per migliorare la resistenza alla corrosione, all’usura e l’estetica dei componenti metallici.
Il problema
L’azienda ha avviato un percorso di digitalizzazione, ma attualmente la schedulazione e la gestione delle commesse si basano sull’esperienza dei responsabili, con strumenti che non permettono di identificare facilmente inefficienze e colli di bottiglia. Le soluzioni attuali sono manuali e testate direttamente in ambiente reale, con rischi di sprechi di risorse e fallimenti.
La soluzione
Il progetto ha visto la creazione di un Digital Twin di un impianto di ossidazione. Questo modello digitale consentirà di simulare il funzionamento dell’impianto, ottimizzare la schedulazione delle commesse, monitorare l’efficienza e ridurre tempi morti e sprechi. Inoltre, permetterà di effettuare analisi predittive su guasti e manutenzioni, riducendo i rischi di fermi impianto non programmati.
Tecnologie
Il progetto ha utilizzato la tecnologia del Digital Twin, sensori per la raccolta dati, piattaforme di analisi e algoritmi di schedulazione avanzati. Le simulazioni di layout produttivo possono così essere eseguite in ambiente virtuale prima di essere implementate nell’impianto reale.
Impatti desiderati
L’implementazione del Digital Twin migliorerà l’efficienza produttiva, riducendo sprechi di tempo, risorse ed energia. Verrà anche ottimizzato l’uso delle attrezzature e delle materie prime, garantendo il rispetto dei tempi di consegna e migliorando la qualità del prodotto.
Benefici per l'impresa
Il progetto migliorerà la competitività aziendale grazie alla riduzione di inefficienze, il controllo dei costi e l’aumento della capacità produttiva. La simulazione predittiva permetterà di prevenire fermi macchina e guasti, con un impatto positivo sulla qualità e sostenibilità del processo.
Contenuti Correlati
-
Modulo 4 – Digital Transformation: Cosa vuol dire essere aziende data driven
-
Modulo 1 – Percorso Digital Transformation: Trend del manifatturiero
-
Percorso Digital transformation
-
Modulo 5 – Digital Transformation: Cosa vuol dire diventare un’azienda sostenibile
-
Modulo 3 – Percorso Digital Transformation: Gestione del cambiamento all’interno delle aziende
-
Modulo 2 – Percorso Digital Transformation: Analisi, costi e benefici dell’introduzione di nuove tecnologie.
-
Percorso Generative AI
-
Percorso Digital transformation
-
Modulo 5 – Digital Transformation: Cosa vuol dire essere aziende data driven
-
Modulo 4 – Digital Transformation: Cosa vuol dire diventare un’azienda sostenibile
-
Logistica 4.0: le nuove tecnologie a supporto della pianificazione e della gestione dei magazzini
-
Digital twin per i sistemi logistico-produttivi
-
Digital Twin di processo
-
Additive Manufacturing
-
L’intelligenza artificiale a supporto delle Operations
-
Progettazione 4.0
-
Manifattura 5.0
-
Monitoraggio intelligente della qualità stradale
-
Innovazione Digitale per Supervisione SMART e Gemello Digitale nel comparto delle macchine accoppiatrici
-
Implementazione Digital Twin in ambito logistico-produttivo stabilimento SOCOMEC di Isola Vicentina
-
Digital Twin di un impianto di ossidazione
-
Tecnologie per la macinazione del caffè
-
BCU (Basic Control Unit) – Evoluzione linea Carel
-
CUSTOMIZATION CENTER DIGITAL TWIN- CC –TWIN
-
WOW
-
VIR-PRO-DE
-
DIGITbreak
-
SmartColeSoleHand
-
EDAP